Gleeble Flow Stress Testing Optimizes Processes and Maximizes Yield
Emerging Technology
Author: Austin Dicus
The hot workability of a particular alloy is crucial to successful processing. Generally, the higher the hot ductility, the easier an alloy will process (forge, roll, etc.). An alloy with less than sufficient hot workability will experience cracks, hot tears, and other forging defects, which can ultimately lead to lower yields or scrapping of complete ingots. This, of course, can be extremely costly for both Carpenter Technology and our customers.
To make sure an alloy has sufficient hot workability prior to full-scale production, lab-scale physical simulations are employed. Thermomechanical physical simulations allow R&D engineers a snapshot into how an alloy will perform during hot working and what forging conditions to target to guarantee a higher quality final product.
Hot Workability: Gleeble 3800
With the use of a Gleeble 3800, the hot workability window can be identified via isothermal hot tension tests. This physical simulation can be adjusted to account for different processing techniques common at Carpenter Technology. When a legacy or experimental alloy’s hot workability is evaluated, an alloy’s critical properties, such as maximum hot ductility, nil ductility temperature, and nil strength temperature, can all be measured prior to processing.
Typical guidelines:
- Less than 30% reduction in area (RA) - poor hot workability - abundant defects
- 40-60% RA - acceptable hot workability - few/very few defects
- Greater than 70% RA - superior hot workability - defects are rare
Results help identify a hot workability window. Based on these recommendations, the processing route can be adjusted to increase the yield and quality of product for a given alloy or process.
Flow stress testing
Flow stress data is obtained by completing hot compression tests and is used in thermomechanical simulation software to model a particular product form, process, or alloy. These models can be utilized to optimize or create new processing routes and help maximize yield. Thus, the end results of utilizing such models are lower costs and higher quality materials.
A material’s flow stress is defined as a material’s instantaneous level of stress required to continue plastic deformation at a constant strain rate. Flow stress is an extrinsic property that depends on the temperature and strain rate. This material property can be experimentally tested via thermomechanical physical simulations. At Carpenter Technology, we use a Gleeble 3800 unit to test isothermal conditions at a wide range of strain rates and temperatures, which correlates to common metal working processes.
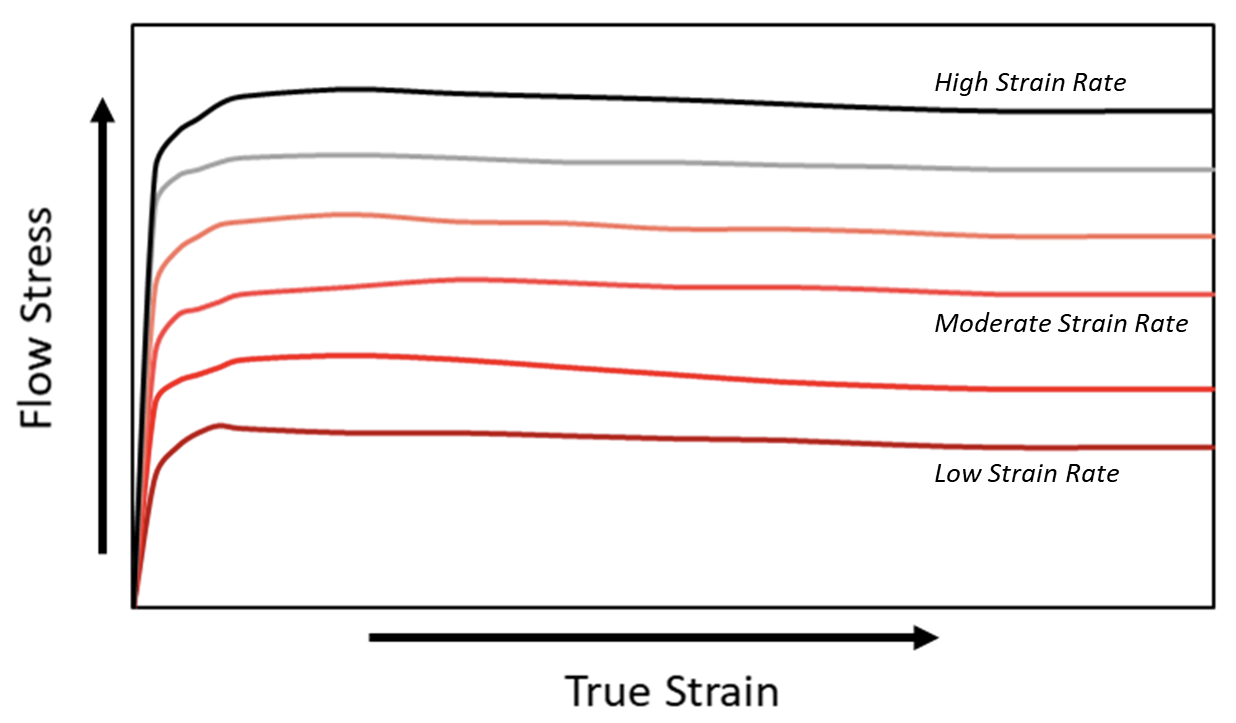
Adiabatic Heating
Some metal working processes, due to their higher strain rates, produce a non-trivial amount of adiabatic heating. The level of heating in some cases can lead to an increase in alloy temperature of >50°F. This increase can be detrimental to alloy processing and lead to defects and/or scrapped material. The level of adiabatic heating can be measured and corrected using the Gleeble system. Once a legacy or experimental alloy is tested, the flow stress data is corrected for adiabatic heating, then uploaded to thermomechanical simulation software to model the exact processing techniques, parameters, and constraints. Finally, the process parameters highlighted by the model are adapted and used in full-scale production to help manufacture a higher quality hot worked product.
![]() |
|
If you have any questions regarding our Gleeble flow stress testing, our expert team would be happy to assist you.